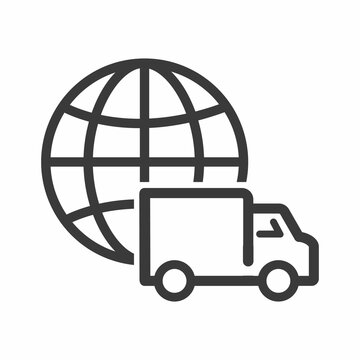
Too much of the shipping operations and material handling is still manual, inefficient and sub-optimized.
Automated, single pane of glass that integrates data from multiple databases to optimize container packing and quickly tracks and traces lost packages.
Improved container management and route logistics to reduce costs. Improved customer service and reduced customs fines by finding mishandled, incorrectly routed, or lost packages before it’s a problem.
The existing shipping and logistics process for this global shipping giant was not accurately tracking shipments and they were failing to optimize shipping container loading and rout logistics. This resulted in higher costs and increased risk to the reputation of the business.
Finding mishandled, incorrectly routed, or lost packages was a manual and time-consuming process. And the longer it takes to find a lost package, the greater the risk of fines and insurance claims – not to mention the damage to the company’s reputation. Custom Agency fines are imposed when a shipping manifest doesn’t match the contents of the shipping container or when lost packages end up in the wrong destination country. Insurance claims are paid out when packages cannot be found. Staffing and overtime costs were spent searching and retrieving lost packages manually. The magnitude of the problem is big. Hundreds of packages go missing each day.
Although operations are highly automated, too much of the shipping operations and material handling was still manual, inefficient, and sub-optimized. It was bad enough that it was hard to find lost packages and prevent customs fines and insurance payouts. Even when packages did make it to their destination, containers were rarely as full as they could be, and shipping routes were rarely cost-optimized. Previous efforts to improve operational efficiencies delivered short-sighted gains in isolated areas. But now, too many sources of good information had to be correlated manually. As a result, these multiple systems and databases created a serious obstacle to achieving the gains in overall operational efficiencies to match – and surpass – their global peers and competitors.
These issues had a ripple effect throughout the business. For example, the inefficient shipping process was preventing them from achieving their environmental sustainability goals.
Hitachi Digital Services worked with the client to establish a criterion to improve the shipping process through automating manual processes, integrating databases and systems, and providing an efficient and actionable single-pane-of-glass to find packages faster and to optimize container loading and route optimization.
The solution focused heavily on reducing human touch points and manual decisions for tracking and tracing lost packages, piecing together information from multiple databases, and optimize container packing. It streamlined package retrieval and reduced the time spent searching for lost packages. And it improved tracking systems to minimize losses.
The wholistic approach of automation of processes and integration of data resulted in operational improvements to a wide range of operational aspects of the company. It ensured accurate package delivery to the right destination and implemented measures to proactively address actions that could result in customs fines. It optimized shipping container efficiency and improved the container loading processes for fuller containers which reduced wasted space and cut shipping costs. The solution also addressed ways that this data driven approach could enhance package security by implementing measures to prevent theft and loss by utilizing technology for secure package tracking. A side benefit was that the solution made it easy to provide much needed information to government agencies focused on smuggling and illegal activity.
Utilizing Advisory Services, Consulting Services, Custom Implementation and Delivery Services, Hitachi Digital Services boosted operational cost-efficiency and introduced technologies to reduce manual labor and optimize processes for overall cost savings. The solution improved customer experience by ensuring timely and accurate package delivery and enhancing the tracking and notification systems for our client’s customers. The solution provided a single pane of glass that integrated systems and databases to provide a more complete and detailed view of the journey or each package.
Hitachi designed, implemented, and integrated an improved process for tracking lost packages and optimizing shipping logistics for efficiency that utilized Hitachi Visualization Suite (HVS) at multiple locations within the logistics facility. A key part of the solution was accomplished by integrating HVS and the customers’ existing video management system along with multiple databases, and deployed hardware (edge gateways, barcode scanners, LED bar strips, etc.). Hitachi’s 3D Lidar-based solution data was also used to automate and optimize the shipping process. And finally, Hitachi trained the staff to utilize and apply this new technology to maximize packaging volume and spacing.
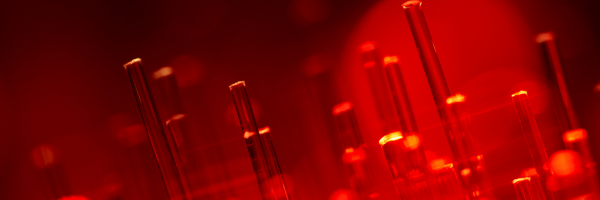
As a result of Hitachi Digital Services’ engagement, our client realized an immediate reduction in operating costs, and dramatically faster and easier process to find mishandled, incorrectly routed, or lost packages. The client is now able to have the operator input lost package label information and quickly connect to the archived video of the nearest camera to locate the package, thus saving hours of manual review.
After the initial months, the client was able to see reduced fines from Customs Agencies and Insurance claims as well as reduced cost of shipping operations. They attribute this directly to a more efficient container volume management and improved logistics and route management.
Ultimately the client was able to track an 85% reduction in time to find lost packages and approximately 60% reduction in labor costs for searching for lost packages. They are confident that this new process, utilizing advanced technologies and the integration of systems and databases will lead to 45% reduction in Customs fines and Insurance claims and an increase in speed and accuracy in providing data to govt agencies policing smuggling, and illegal activities.