August 19, 2024
Global steel production has more than tripled over the past five decades. China and India have become the top two steel producing nations jointly contributing around 60% of the global steel production. The industry has witnessed significant technological advancements, leading to higher productivity, improved product quality, and increased flexibility in the product mix by introduction of multiple steel alloys. These advancements along with initiatives to improve operational efficiency, waste reduction through application of lean concepts and quality improvement initiatives have resulted in higher productivity and made operations more sustainable. Most of the steel producing organizations globally and in India as well have leveraged these transition phases effectively to attain higher profitability.
Why workforce productivity?
For a long period, as the industry has moved towards technology adoption and operational excellence, these levers remained in focus for enhancing productivity. As these levers gained maturity and the scale of production increased, the focus was to achieve higher workforce productivity to boost the profit margin further.
This resulted in organizations focusing specifically on workforce productivity and it became a strategic KPI for large steel producers globally and in India. In India, in the last decade, there has been significant progress on workforce productivity. Organizations are embarking on focused programs to enhance workforce productivity which remains crucial for safe, sustainable, and profitable operations.
Measuring workforce productivity
125MT
Steel production in 2022
makes India second largest steel producer in the world
250-520
Tons/Employee*/Year
Productivity is observed across different
organizations withn the country.
*All types of emplovees are considered based on annual
reports of top steep producers of India.
Figure 1: Steel production in India and productivity of top steel producers
profit margin.
Figure 2: Productivity enhancement in last decade across three top steel producers of India.
Typical challenges organizations face in measuring and improving workforce productivity:
Understanding the factors which impact productivity
Workforce productivity in steel depends on various factors which are represented below. Technology deployed and the level of automation along with the age of the asset is the first factor which impacts productivity. Steel plants which have been commissioned recently with advanced technology and higher level of automation will need lesser manual efforts as compared to older plants.
Figure 3: Factors impacting the workforce productivity in steel
Workforce deployment strategy depends on multiple factors but the two key factors driving the decision of deployment are duty positions and workforce availability.
It is imperative for designing an effective workforce deployment strategy that organizations have deep understanding of the work content and duty positions should be defined aligned to that. All the details of the resource available should be documented and then these two aspects should be mapped to create the most effective deployment across the organization.
Figure 4: Variables and complexities in understanding the duty position and resource available
Approach for workforce productivity enhancement
We propose a two-pronged approach for workforce productivity enhancement. The current state helps to get indepth understanding of where we stand and where we want to reach. The future is about detailing out the steps
which will take us to the desired place and then executing those steps.
Figure 5: Approach for effective workforce deployment
Assessment Phase
We propose a two-pronged approach for workforce productivity enhancement. The current state helps to get indepth understanding of where we stand and where we want to reach. The future is about detailing out the steps
which will take us to the desired place and then executing those steps.
The first step of workforce productivity improvement is to understand the current state of the workforce
deployment. It begins with vision alignment on the desired state with leadership, time horizon and resource
commitment. Once we align with leadership, to avoid any bias in mapping the current state it is advisable we
start from the basics and go through below mentioned three steps:
Once the current state map is ready, ideation workshops and Gemba walks are done to identify the opportunities
for improvement. Operational analysis and assessment help in validating the improvement opportunities. Key
improvement levers used during the assessment phase are:
• Process • Automation • Digitization • Outsourcing
Subject matter experts are engaged to share their experiences and best practices from different organizations and lists of improvement initiatives are generated to define the future state roadmap.
Value Realization
To implement the transformation roadmap, the organization should form a cross-functional team which will create a detailed business case by prioritizing all the initiatives suggested in assessment phase. Benefits estimation and investment calculations are done for the approval of each initiative by the leadership before it moves into implementation.
The project team will monitor the progress of respective initiatives and report the value delivered by each initiative.
Sustaining the change
Productivity Center of Excellence
As the organization moves from internal best practices to become benchmark in workforce productivity, it becomes important to have a dedicated team developing the plans, arranging required resources and skills, and delivering the continuous improvement in productivity. Productivity Center of Excellence (CoE) team should be formed with members from different departments to lead the workforce productivity journey.
Periodic Health Check
Post setting up a designated team in place and putting the organization on a continuous improvement journey, a period health check on a quarterly or half-yearly frequency by an external agency or expert helps in staying on track. A third party brings a completely neutral view, shares ideas basis the new reality of the organization and brings on multi-industry and multi organization knowledge
Periodic health check on continuous basis also does a reality check to give the organization a true picture of the progress against the set goal.
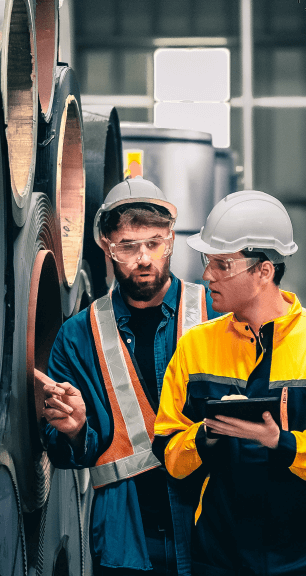
Enhance your Workforce productivity
As the Indian steel producers focus more on workforce productivity, it is pertinent to start from the basics. It is crucial to clearly define the duty positions across the factory considering the steel making process and set guidelines for deployment. The current state is developed by mapping available resources against the duty positions. A clear and transparent picture of the current state will help in setting realistic goals and preparing a roadmap to achieve the desired state. Hitachi’s Industry Consulting Practice drives your workforce productivity improvement journey by assessing your current state in terms of workforce productivity, helping your organization discover improvement areas by applying 4 levers and recommend initiatives that will help reach the desired state. To schedule time with our workforce productivity subject-matter experts and ask for a workforce productivity assessment for your operations, please reach out to us at manufacturing@hitachids.com
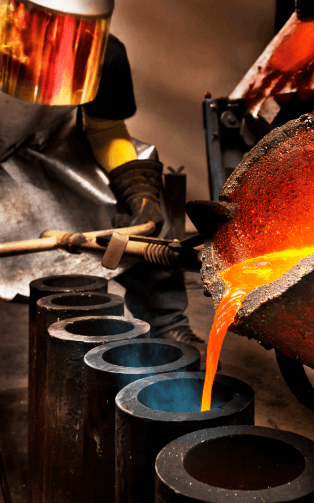